Sealing System Leakage Analysis - Shaft
Shaft Diameter
Probable Causes | Actions or Countermeasures |
---|---|
Oversized shaft may accelerate lip wear, increased heat generation, shaft wear and may cause lip to invert during installation. | Replace shaft, if oversized, machine to proper diameter. |
Undersized shaft may result in insufficient lip interference to seal properly, resulting in premature leakage. | Replace shaft, if oversized, machine to proper diameter. |
Shaft Surface Roughness (Primary Sealing Surface)
Probable Causes | Actions or Countermeasures |
---|---|
Excessive rough shaft may accelerate lip wear and if too rough, leak upon initial startup. | Apply proper surface roughness. |
Excessively smooth shaft may accelerate lip wear and increase heat generation. | Apply proper surface roughness. |
Shaft Corrosion
Probable Causes | Actions or Countermeasures |
---|---|
Corrosion on the shaft in the area of the lip contact point will interfere with the lip's ability to seal against the shaft surface properly. The increased surface roughness may provide leakage paths and lip wear may increase from higher roughness. | Apply corrosion resistant shaft material. |
Use replaceable corrosion resistant shaft sleeve. | |
Change assembly design to limit access of corrosive contaminates. | |
Change to seal design that will protect shaft from corrosion so seal lip can function normally. | |
If corrosion from inventory storage before assembly - change inventory system. |
Lip Wear Band in Wrong Location on Shaft
Probable Causes | Actions or Countermeasures |
---|---|
Insufficient or excessive lip interference may occur which will affect lip's ability to seal. | Check to make sure proper seal is being used (is the width to spec.?) |
Improper seal of seal lip may contact shaft resulting in high temperature or leakage due to improper lip orientation. | Check to make sure seal was installed to proper depth (not too deep or not enough depth). Installation tool procedure may need to be revised to ensure proper depth. |
Check shaft or total assembly per specification to see if correct | |
If seal moving after installation? Check installation method and seal and bore diameters. Is pressure a problem? | |
If metal case of seal is deformed during installation, may orientate lip improperly. |
Scratches or Nicks at Lip Contact Area on Shaft
Probable Causes | Actions or Countermeasures |
---|---|
Scratches or nicks (if large enough) across the seal contact area of shaft will act as leakage paths. | Check handling procedures of shaft from time shaft is machined until it reaches assembly area - special carrying trays which protect shafts from hitting each other is suggested. Special cardboard or nylon mesh sleeves are commonly used. |
Is shaft damage during actual assembly? May require assembly method change or jig change. | |
Does worker mishandling cause damage? Improve handling method. | |
It may be possible to rework shaft to remove defect but shaft roughness or diameter should not be altered outside of design spec. | |
Harden shaft to minimum RC45 to improve resistance to scratching or nicking. |
Excessive Shaft Wear
Probable Causes | Actions or Countermeasures |
---|---|
Seal lip will have difficulty sealing against the shaft wear band if the depth is too large or width is too wide. | Check shaft hardness. May require hard shaft. |
Is outside contaminant ingestion causing problem? Use a contaminant resistant seal design. | |
Improper lubrication can cause accelerated shaft wear. Check lubricant compatibility with lip and quantity of lubricant reaching seal. | |
Is contaminant present in the fluid to be sealed? Check compatibility and change fluid more often or filter more effectively. | |
Proper lip interference: Check shaft diameter and seal to make sure to spec. | |
Excessive eccentricity can cause unusual wear. Check for excessive runout or shaft to bore misalignment. |
Wide Shaft Wear Band Relative to Seal Wear Band
Probable Causes | Actions or Countermeasures |
---|---|
Leakage may result prematurely as lip cannot maintain proper orientation against the shaft. | Check for seal cocking and correct installation procedure if found. |
Leakage may occur as wide shaft wear band may act as leakage path. | Excessive axial motion can cause this type of wear. Check assembly and replacing bearings if defective or worn. |
Below is an extreme example of seal cock.
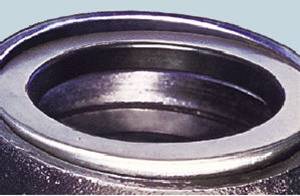
Shaft Discoloration or Coked Oil on Shaft
Probable Causes | Actions or Countermeasures |
---|---|
Discoloration may indicate excessively high temperatures. The high temperature may effect other characteristics of seal (i.e. Lip hardness) which will result in premature failure. | Check quantity of lubricant reaching seal and increase if necessary. |
Coked oil buildup will interfere with the seal lip's ability to contact shaft which will result in premature failure. | Was shaft diameter or lip IP causing too much interference? Change to reduce interference. |
Bearing preload too high causing temperatures in seal area to be very high. Set bearing to proper preload. | |
Shaft too smooth causing seal to run hot. Check shaft roughness. | |
Excessive pressures in seal cavity can load seal lip excessively against shaft causing high temperatures. Reduce pressure or use pressure resistant seal design. | |
Change oil to high temperature resistant fluid. | |
Reduce operating temperature of final assembly to range compatible with lubricant and seal material. |
Machine Lead
Probable Causes | Actions or Countermeasures |
---|---|
Machine lead may hydrodynamically pump medium to be sealed out depending on shaft rotation direction. | Finish shaft as recommended to eliminate machine lead. Plunge grinding is typically the best method to completely shaft lead. |
Below is the standard test for identifying shaft lead. The maximum allowable lead angle is <0+/-0.05
Shaft Hardness
Probable Causes | Actions or Countermeasures |
---|---|
Shaft with hardness less then RC 30 way experience accelerated wear, especially if sealing in a highly abrasive environment. | Harden shaft or use harder shaft material. |
RC 45 is the preferred hardness if handling defects (scratches of nicks) are likely. | Use wear sleeve. |
Reduce amount of contaminants reaching seal by changing to contaminant resistant seal design or changing assembly design to limit outside contaminants. Change fluid more frequently if inside contaminants. Using better wear resistant bearing, gear or other metal components inside assembly will help reduce contaminants in lubricant. |
Shaft Chamfer Condition
Probable Causes | Actions or Countermeasures |
---|---|
Insufficient chamfer may cause seal lip to invert, cause garter spring to pop off or make installation very difficult. | Apply proper shaft chamfer as recommended, 0.45 deep and 15-30 degree lead in angle. |
Sharp edges or burrs may cut seal lip or cause lip to invert. | Use a shaft sleeve, mandrel or bullet to protect seal lip during installation. |
Below is an example of a seal that has been installed on a shaft without the proper lead in chamfer.
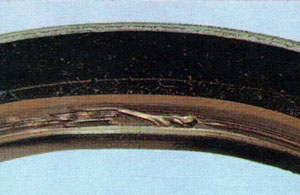
Proper Shaft Material
Probable Causes | Actions or Countermeasures |
---|---|
Primary concern is achieving recommended shaft hardness and/or resistance to corrosion if in a highly corrosive area. | Change shaft material to compatible material for application. |
Shaft wear sleeve may be applied. |
Below is an example of a seal that has been installed on a shaft without the proper lead in chamfer.
Wear Sleeve Fit
Probable Causes | Actions or Countermeasures |
---|---|
Improper fit of the sleeve may result in a deformed sleeve. | Follow proper installation methods to insure sleeves is not damaged during installation. |
Leakage may occur between sleeve ID and shaft diameter. | Check shaft chamber for burrs or nicks or improper angle/depth and correct. |
If sleeve is loose, it may rotate separate from shaft resulting in excessive heat generation. | Use additional sealant to prevent sleeve ID/Shaft interface leakage. |
Check shaft diameter OD/sleeve ID to see if correct - replace if necessary. Also sealant such as loctite or permatex may prevent sleeve from spinning. |
Login
News
February 23rd
Here is a great article on grease compatibility . . .
The Skinny on Grease Compatibility
July 30th
Here is a link to a great article about how to avoid particulate contamination . . . Obviously it goes without saying that a sealing...
How to Avoid Particulate Contamination